SOLIDWORKS SimulationXpress je simulacijski modul, ki deluje na principu metode končnih elementov. Omogoča vam preračun preproste analize kosa z enim telesom. SOLIDWORKS SimulationXpress je vključen v vsaki verziji SOLIDWORKS-a (tudi v SOLIDWORKS Standard in SOLIDWORKS Professional).
SOLIDWORKS SimulationXpress lahko najdete pod “Tools“:
Klub temu, da je SOLIDWORKS SimulationXpress vključen v vseh verzijah SOLIDWORKS-a, ga je za uporabo potrebno še aktivirati. Postopek aktivacije je prikazan na našem forumu na sledeči povezavi: https://forum.ib-caddy.com/viewtopic.php?f=4&t=297&p=476
Uporaba SOLIDWORKS SimulationXpress-a
Ko je SOLIDWORKS SimulationXpress aktiviran in zagnan, se pojavi SimulationXpress čarovnik v Task Pane panelu na desni strani ekrana. Čarovnik vas vodi skozi nastavitve in pogon analize. Na ta način lahko tudi uporabniki, ki niso domači v simulacijah, pripravijo analizo po korakih v čarovniku.
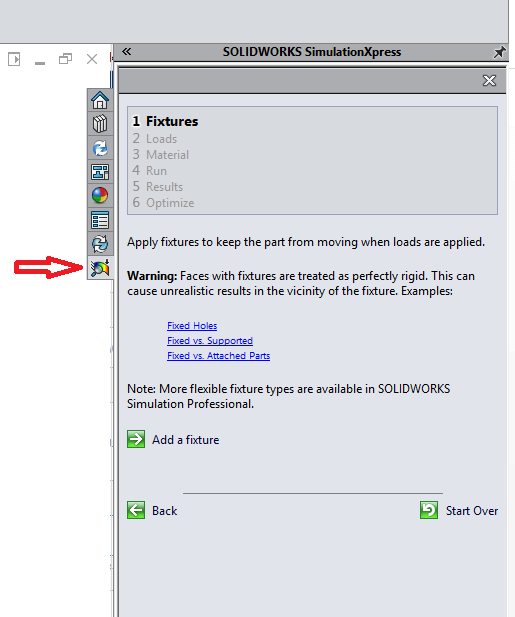
Fixtures – vpetja
Prvi korak pri pripravi analize je določitev kje bo vaš kos vpet v prostor. To je potreben korak, saj bi brez vpetij kos “plaval” v zraku. Vsaj ena izbira mora biti določena. Na sledeči sliki lahko vidimo, da je izbrana ena površina, kjer se pojavijo zelene puščice, ki nakazujejo, da smo na tej površini omejili vseh 6 prostorskih stopenj.
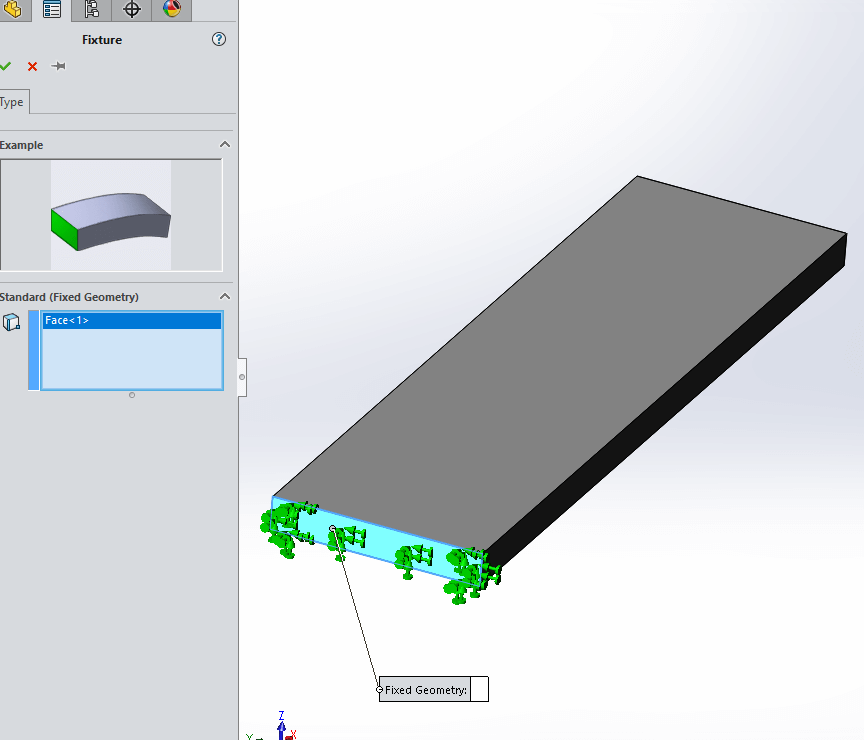
Loads – obremenitve
Drugi korak vključuje definicijo obremenitev. V SOLIDWORKS SimulationXpress lahko definiramo dve vrsti obremenitev – sila in pritisk. Obremenitve definiramo na površine, kjer se pojavijo puščice, ki nakazujejo obremenitev.

Material
Za preračun premikov in napetosti, moramo definirati materialne lastnosti. To pomeni, da moramo definirati material. SOLIDWORKS SimulationXpress preračunava samo linearne statične analize – nelinearnih pojavov, kot je plastična deformacija, se ne preračuna.
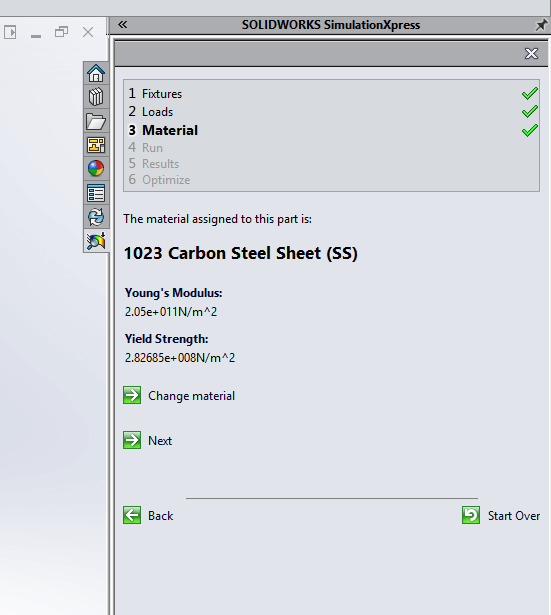
Run – pogon simulacije
Pred pogonom analize, je potrebno določiti mrežo. To vpliva na natančnost rezultatov. Bolj fina mreža pomeni bolj natančne rezultate a bo preračunski čas zato daljši. Mrežo se spremeni pod “Run”→”Change settings”.
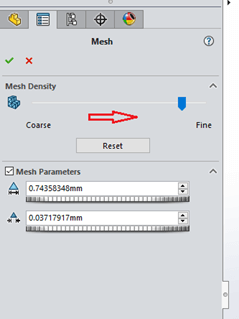
Results – rezultati
Ko se analiza preračuna, vidimo deformacijo geometrije. Ta deformacija je ponavadi skalirana, da se rezultati vidijo čim bolj nazorno. Skaliranost deformacije se vidi v zgornjem levem kotu grafičnega okna.
Tukaj imamo dve možnosti: lahko nadaljujemo ali pa se vrnemo nazaj in spremenimo nastavitev analize. Če nadaljujemo lahko vidimo rezultate deformacije, napetosti in faktorja varnosti.
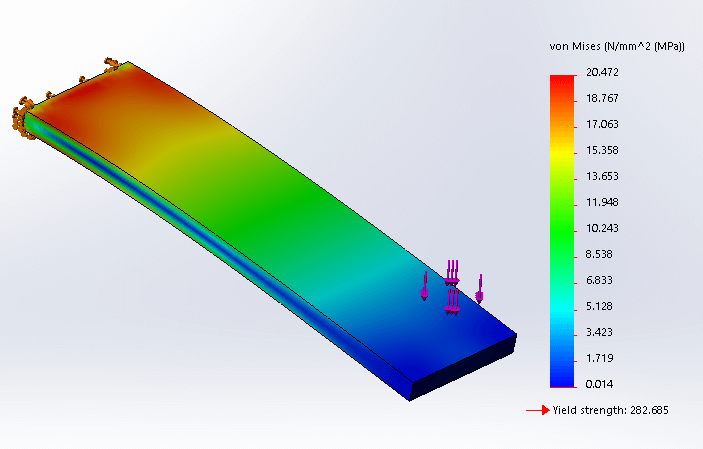
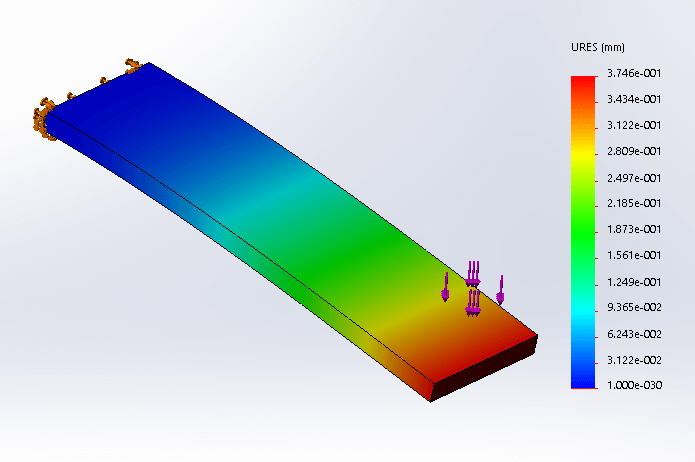
Po pregledu rezultatov, lahko generirate poročilo v Microsoft Word formatu. Model lahko izvozite tudi v eDrawings formatu, da lahko ostali uporabniki, ki nimajo dostop do SOLIDWORKS-a, pregledajo model in rezultate analize.
SOLIDWORKS SimulationXpress je izredno uporabno orodje s katerim lahko htro in preprosto preračunamo vpliv obremenitev na naš kos. S temi podatki lahko izdelamo boljšo verzijo kosa, zmanjšamo število prototipov,… Če moramo pripraviti analizo na bolj kompleksni geometriji, ima SOLIDWORKS v svoji ponudbi bolj napredne simulacijske produkte. Analize v SOLIDWORKS Premium paketu nam na primer že omogočajo preračun obremenitev na sestavih.
Pri simulacijah se je potrebno zavedati, da so rezultati ocene poenostvljenih robnih pogojev in modelov ter jih je potrebno preveriti v realnosti.
Več informacij o Simulacijskih produktih SOLIDWORKS-u lahko najdete na https://solidworks.ib-caddy.com/products/simulation.php