Ken Pillonel, inženir in ustanovitelj priljubljenega YouTube kanala Exploring the Simulation, je imel idejo – oblikoval bi ohišje za AirPods, ki bi ne le zaščitilo slušalke, ampak omogočilo uporabo USB-C priključka za polnjenje namesto starega Lightning priključka.
Pillonela že leta frustrira prisilna zastarelost potrošniških izdelkov in ovire za uporabniško popravljivost. “Zaskrbljujoče je videti oblikovalske odločitve, kot so nezamenljive baterije, zlepljene komponente in pomanjkanje transparentnosti v javnih informacijah, kar vodi v porast ‘hitre elektronike’,” je Pillonel povedal Willu Shanklinu iz Engadgeta.
Zdi se, da Pillonel ni bil edini v svojih frustracijah; ko je napovedal projekt ohišja za polnjenje AirPods, je prejel na tisoče naročil strank z vsega sveta. Da bi izpolnil ta naročila in dostavil tisoče izdelkov – medtem ko je delal iz svojega stanovanja in brez zaposlenih – je Pillonel potreboval proizvodno rešitev, ki bi delovala tako trdo kot on.
“Moj cilj je bil, da čim več svojega razvoja strojne opreme obvladam v hiši, kar mi omogoča, da svoje ideje spremenim v resničnost. S Fuse Series tiskalniki mislim, da sem pripravljen v smislu 3D tiskanja,” pravi Pillonel.
Omejitve tradicionalnih metod proizvodnje
Tradicionalne metode proizvodnje, kot je brizganje plastike, so še vedno (in verjetno bodo še nekaj časa) najcenejši način za množično proizvodnjo večine potrošniških izdelkov, kot je na primer ovitek za AirPods, ki ga izdeluje Pillonel (ali Apple). Najbolj smiselna metoda za velike proizvajalce z vnaprej določenimi količinami povpraševanja in ponudbe. Glavna težava pri manjših proizvajalcih, kot je Pillonel, pa so omejitve, ki jih te metode postavljajo na agilen proces oblikovanja izdelkov.
Za finančno izvedljivost brizganje plastike zahteva popolnoma dokončne ideje in nobenega prostora za izboljšanje oblikovanja, medtem ko je Pillonelova ideja postala privlačna za tisoče kupcev prav zaradi njegove odzivnosti, agilnosti in sposobnosti odzivanja na povratne informacije strank.
Pillonel, ki je dobro seznanjen z zastarelostjo, je prepoznal, da bi vsak kalup, ki bi ga naročil, čez nekaj let postal zastarel, saj bi njegovi kupci prešli na nov tip slušalk in ovitka.
Še ena težava brizganja so oblikovne omejitve, ki jih postavlja proces. Njegovo oblikovanje ovitka je bilo kompleksno, z več geometrijami, ki jih ni mogoče zlahka izdelati v orodju za brizganje. “Obstajajo notranje votline. Obstajajo luknje. Obstaja gravirano besedilo. Če bi želel brizgati ta del, ne bi bil preprost dvodelni kalup. Potreboval bi zelo zapleten kalup z drsniki, zato bi se stroški eksponentno povečali.”
Ena izmed pasti oddaje proizvodnje novega izdelka v tujino je lahko t.i. “ghost shifts” – situacija, ko partnerske tovarne za brizganje plastike v tujini proizvajajo več, kot je bilo dogovorjeno, nato pa preostanek preprodajajo za dodatni dobiček.
Ulivanje uretana — metoda, pri kateri se silikonski kalup napolni s tekočo plastiko, ki se strdi — je bila še ena možnost, vendar kalupi zdržijo le približno 50 ponovitev, zato rešitev ni bila skalabilna.
S prenosom 3D-tiskanja v svojo delavnico je Pillonel ohranil popoln nadzor nad oblikovanjem, proizvodnjo, nadzorom kakovosti, izpolnitvijo in podporo izdelku.
FDM, SLA, tradicionalno brizganje ali nekaj drugega?
Pillonel že več let uporablja 3D-tiskanje z modeliranjem s spajanjem slojev (FDM) in stereolitografijo (SLA), pri slednji uporablja Form 3+ namizni tiskalnik. Medtem ko verjame, da ima vsaka tehnologija svoje mesto v določenih situacijah, je imel pomisleke glede tega projekta z uporabo FDM ali SLA.
Po prototipiranju s svojimi FDM 3D-tiskalniki se je Pillonel odločil raziskati druge možnosti za končni izdelek. “Začel sem z najcenejšo metodo, ki jo poznam, to je FDM tiskanje s filamentom, vendar sem si rekel, da ne bo dovolj dobro za moj izdelek … ni dovolj dobro za potrošniški izdelek, ki bi ga lahko prodali v trgovini. Preprosto nima vrhunskega občutka,” pravi Pillonel.
S svojim SLA Form 3+ tiskalnikom je imel manj pomislekov glede kakovosti in površinske obdelave, vendar več glede poteka dela. Čeprav je bil zadovoljen s kakovostjo in obdelavo smolnih delov za prototipiranje, ni bila izvedljiva rešitev glede na obseg naročil, ki jih je moral obdelati.
Za kompleksno oblikovanje, ki vključuje gravirano besedilo, ozke kanale, podreze in tanke stene, je potreboval metodo proizvodnje, ki bi to omogočila.
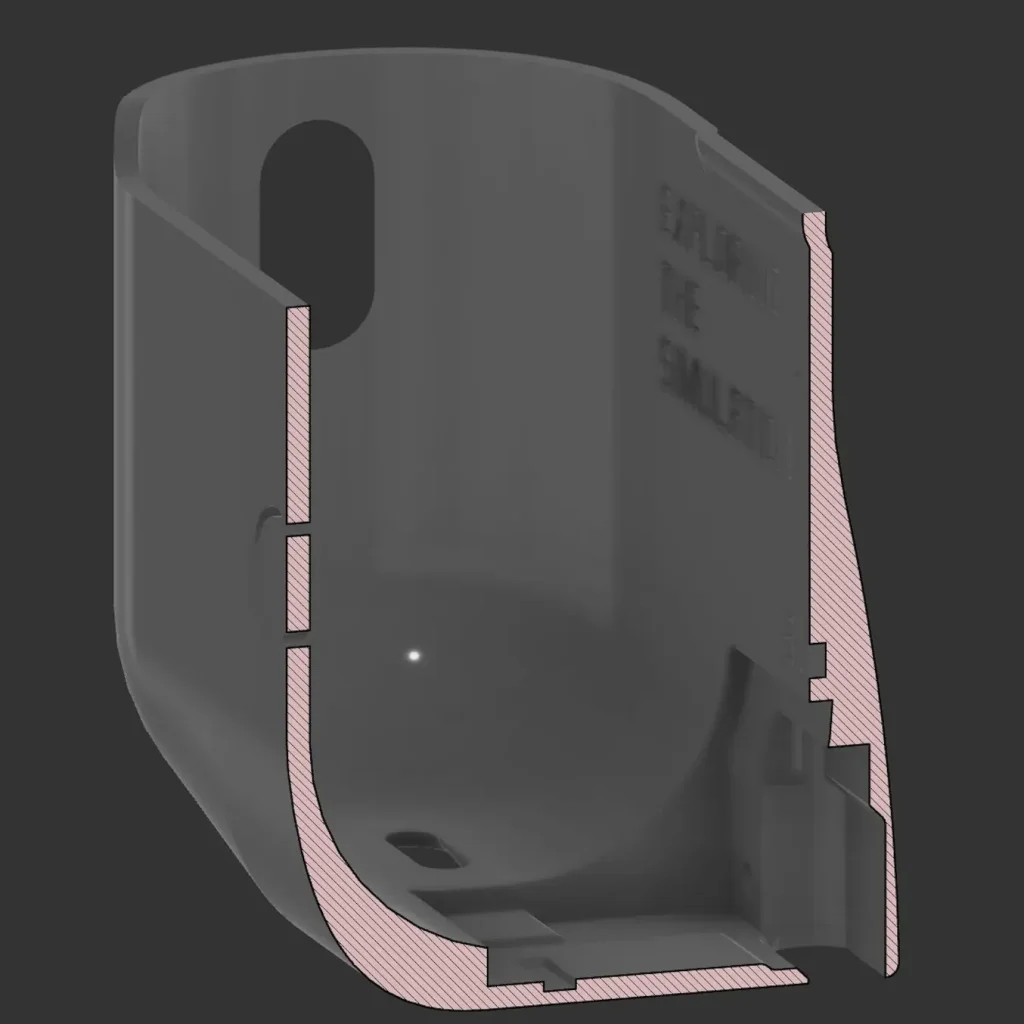
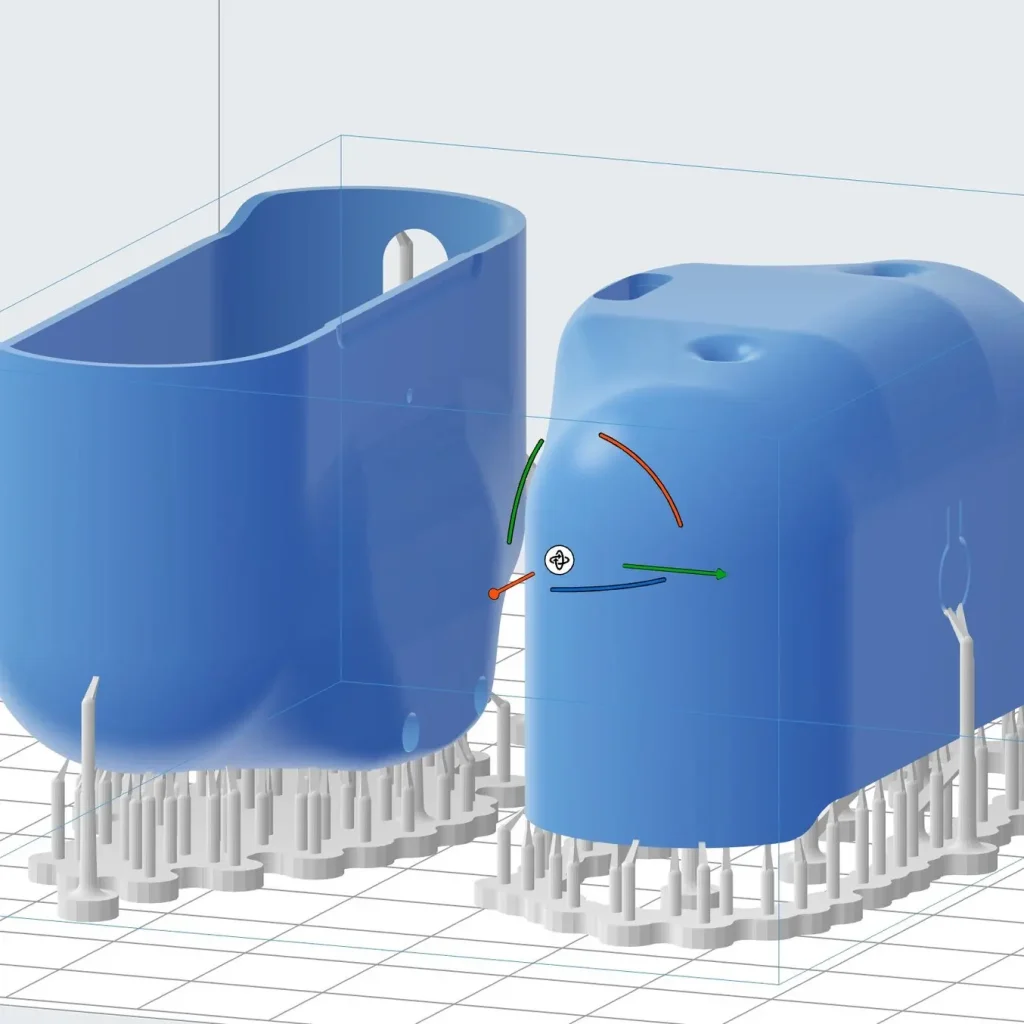
Ukrivljene, organsko oblikovane površine, kot so te, je še posebej težko natisniti na 3D-tiskalnikih FDM, ker lahko pokažejo bolj očitne črte plasti. Pillonel je potreboval proizvodno metodo, ki bi zlahka izvedla kompleksno zasnovo, ki vključuje vgravirano besedilo, ozke kanale, negativno geometrijo in tanke stene.
Za 3D-tiskanje končnih delov je bila edina možnost selektivno lasersko sintranje (SLS). Samonosilna narava prašne postelje odpravi potrebo po podporah, medtem ko mehanske lastnosti najlona zagotavljajo, da bodo ovitki dovolj trpežni za vsakodnevno uporabo. Tehnologija SLS omogoča tudi zlaganje delov enega na drugega v komori, kar pomeni, da lahko Pillonel izdela na stotine delov dnevno z enim tiskalnikom.
Njegov edini zaposlen: tiskalnik Fuse 1+ 30W
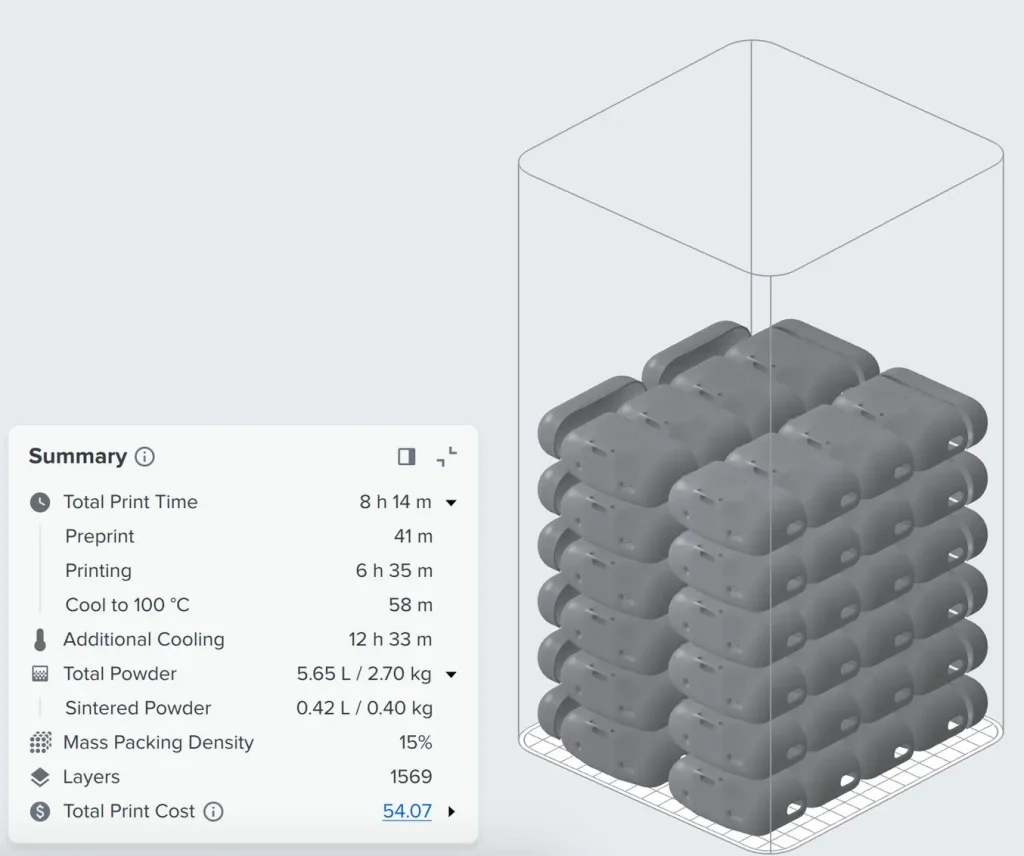
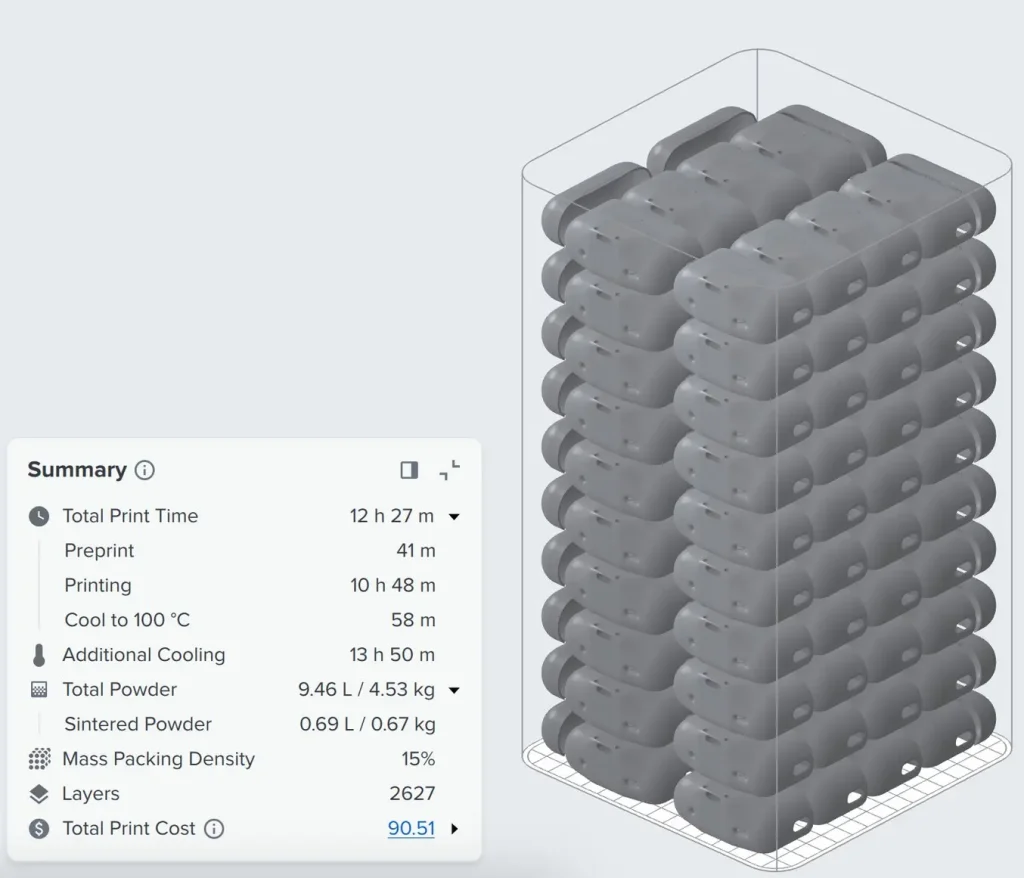
Pillonel uporablja dve delovni komori, da kar najbolje izkoristi svoj delovni proces. Prvo komoro začne uporabljati zjutraj, pri čemer zapolni le polovico njene zmogljivosti, da se tisk zaključi do konca dneva. Ko na koncu delovnega dne vzame prvo (napol zapolnjeno) delovno komoro, začne čez noč tiskanje s popolnoma zapolnjeno komoro, ki bo pripravljena naslednje jutro. Njegov edini zaposlen, Fuse 1+ 30W, dela neprekinjeno!
Ko je prišel čas za “zaposlitev” njegovega edinega zaposlenega, Pillonel ni mogel računati na svoje FDM ali SLA tiskalnike za količino naročil, ki so se kar naprej množila, in tradicionalna izdelava, kot je brizganje plastike, je bila izločena. SLS je bil edina rešitev, a potreboval je dostopno rešitev, ki bi še vedno omogočala izdelavo končnih izdelkov visoke kakovosti.
Na trgu je več možnosti za SLS 3D tiskanje, vendar skoraj nobena ni cenovno dostopna za nove podjetnike ali posameznike. Pillonel je ocenil, da so poceni možnosti preveč nezanesljive, medtem ko so bile tradicionalne možnosti, kot so veliki MJF stroji, predrage in prevelike, da bi jih spravil v svoje stanovanje, kjer ima delavnico. Čeprav je priznal, da serija Fuse ni dovolj cenovno dostopna za hobi ali večino posameznikov, je vedel, da bo to najboljša možnost za povrnitev njegove naložbe.
Pillonelov začetni komplet je bil Fuse 1+ 30W tiskalnik, ena delovna komora in Fuse Sift, skupaj z 12 kg praška Nylon 12. Tudi ob popolnoma industrijsko kakovostnem SLS ekosistemu je lahko Pillonel v nekaj urah varno in enostavno pripravil vse v svojem stanovanju za začetek proizvodnje.
“Po razpakiranju in priklopu naprav sem lahko začel začetno namestitev, ki se je izkazala za zelo enostavno. Preprosto sem sledil navodilom na zaslonu in to je bilo to,” pravi Pillonel.
Bil je čas za začetek proizvodnje, in po samo nekaj mesecih oblikovanja, nekaj testnih serijah popolnoma zapolnjenih komor in prvih povratnih informacij strank, je lahko Pillonel začel resno proizvodnjo, pošiljati dele in optimizirati svoj proizvodni proces.
Priporočila za proizvodne količine
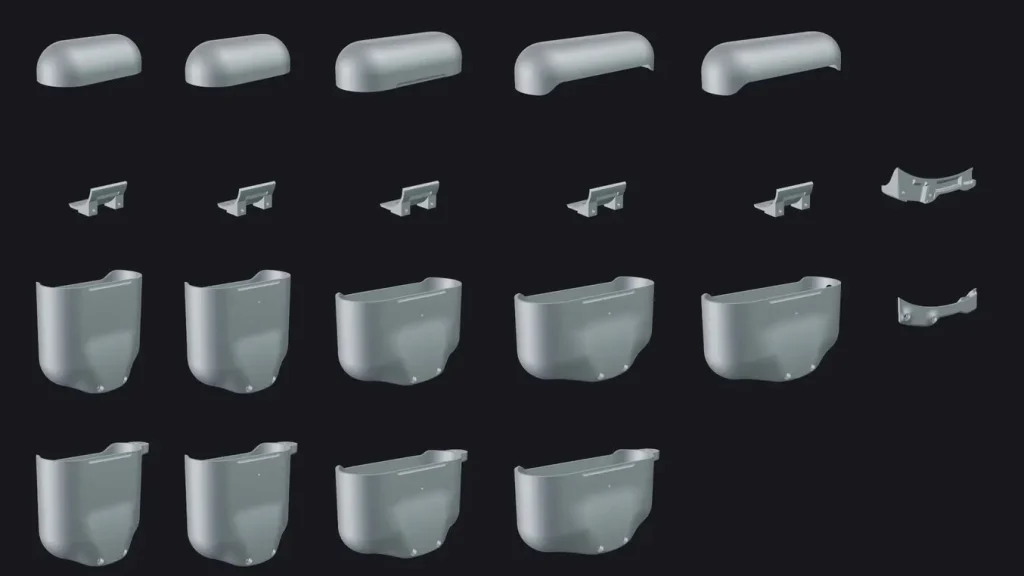
Pillonel ponuja več različic svojega izdelka, nekatere s funkcijami za vrvico, teksture ali nekoliko različnimi priključki. Število različic izboljšuje izkušnjo strank in povečuje vrednost izdelka, vendar otežuje organizacijo proizvodnje, procesiranja in sistemov dostave.
Po tiskanju s Fuse 1+ 30W in celotnim Formlabs SLS ekosistemom, so Pillonelove glavne ugotovitve in priporočila za proizvodnjo končnih izdelkov s serijo Fuse:
- Ohišje za rokavice: Fuse Sift Glovebox je dodaten pripomoček za Fuse Sift (sistem tiskalnika za reciklažo in ponovno uporabo praška). Fuse Sift se lahko uporablja brez ohišja za rokavice — negativni zračni tlak in sesanje dobro preprečujeta dodatnemu prašku, da bi zašel v delovni prostor — a Glovebox prinaša dodatno zaščito in zanesljivost. “Resnično priporočam nakup dodatka Glovebox, ker nekako zapre Sift. Prej ga nisem imel in vedno me je skrbelo, da bom odprl okno in bo prišel veter in v moji delavnici odpihnil nekaj prahu,” pravi Pillonel.
- Pakirajte čim bolj gosto. Gosta zapolnitev delovnih komor zmanjšuje stroške na del. Cilj naj bo zapolnitev komor skladno z osvežitvenim razmerjem vašega praška — tako lahko nesinterirani prašek ponovno uporabite, zmanjšate odpadke in stroške materiala le na to, kar izdelek sam zahteva.
- Zaklenite usmeritev med oblikovanjem in proizvodnjo. Med iterativnim oblikovanjem in testiranjem je smiselno preizkusiti različne usmeritve — lahko vidite, kako usmeritev tiska vpliva na toleranco po delih in kje želite optimizirati čas tiskanja proti gostoti zapakiranja, zlaganje, ohišja delov itd.
- Primerjajte ročno pakiranje z avtomatskim pakiranjem. Avtomatsko pakiranje je učinkovito, vendar ročno pakiranje lahko pri nekaterih situacijah izboljša gostoto za nekaj odstotkov.
- Naredite eno popolno serijo svojega tiskanja na koncu razvojnega cikla. Tako se prepričate o napakah in optimizirate naslednje cikle tiskanja brez zapravljanja materiala.
- Izračunajte optimalen proizvodni urnik in stroške elektrike. Pillonel je našel način, da tiskalnik nenehno deluje z minimalnimi stroški.
- Testirajte optimalno post-obdelavo s Fuse Blast. Ločite dele podobne velikosti in jih obdelajte v kratkih ciklih za najboljše rezultate.
Naslednji koraki za Exploring the Simulation
Pillonel še vedno prejema in izpolnjuje naročila za svoje polnilne ovitke za AirPods, medtem pa njegov ekosistem Fuse Series dela neprekinjeno — tako kot on — kot en sam človek za oblikovanje, proizvodnjo, podporo strankam in izpolnjevanje naročil. Pogled v prihodnost razkriva nekaj vznemirljivih projektov, med drugim raziskovanje metod barvanja in morda celo nekaj novih izdelkov.
Ekosistem Fuse Series je omogočil, da se je Exploring the Simulation razvil od ideje za nov izdelek do popolnoma vzpostavljenega proizvodnega procesa. 3D-tiskanje, zlasti zmogljivo in dostopno SLS 3D-tiskanje, je ustvarilo rešitev za vsaj del problema prisilne zastarelosti v sodobni tehnologiji.
Če želite izvedeti več o Pillonelovem procesu, si oglejte celoten webinar ali zahtevajte vzorec enega od Formlabsovih SLS praškov in sami preizkusite kakovost.
Vir: https://formlabs.com/eu/blog/one-man-plastics-factory-fuse-sls-formlabs-ken-pillonel/