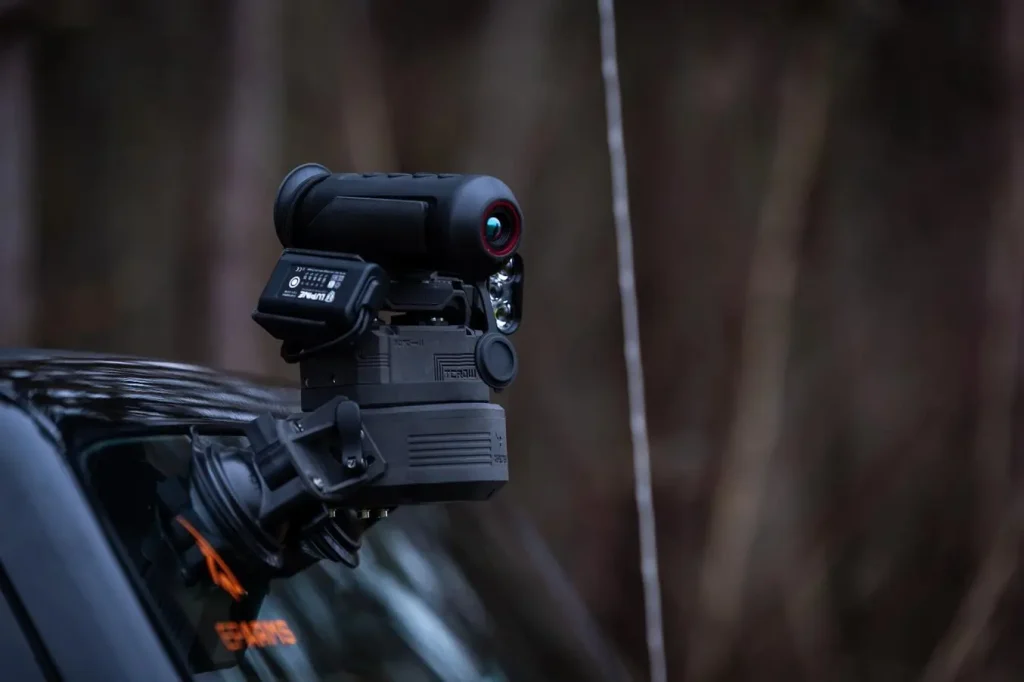
Z inovativno idejo in veliko motivacije je mnogim podjetnikom že uspelo zapolniti vrzeli na trgu. Potem ko ni mogel najti ničesar podobnega, je Matthias Mähler dobil idejo, da bi izdelal prvi prototip posebnega stojala za kamero za nočno opazovanje in ročne termalne slikovne naprave.
Eden glavnih izzivov je bila izvedba zapletene zasnove izdelka, ki bi zahtevala začetno naložbo več kot 100.000 € v orodje, če bi se odločil za brizganje. Brez predhodnega znanja o tem, kako bo izdelek deloval na trgu, bi bilo to za majhen startup zelo tvegano. Z uporabo 3D-tiskanja pri razvoju in kasnejši izdelavi stativa pa se je bilo mogoče izogniti tej veliki investiciji. Zdaj njegovo podjetje XSPECTER izdeluje svojo stojalo za kamero T-Crow XRII in ga uspešno prodaja prek ekskluzivnega partnerja.
V članku boste izvedeli, kako je mogoče izdelati končni izdelek s kombinacijo različnih tehnologij 3D-tiskanja in zakaj se je podjetje XSPECTER odločilo za ta postopek.
Razvijanje stojala za 360° nadzorovano kamero
Naprave za nočno opazovanje in ročne termovizijske naprave so standardna oprema za lovce, navtike in v varnostni industriji. Težava: naprave ne delujejo skozi steklene površine. Pri vožnji avtomobila ponoči to pomeni, da morajo vozniki z roko držati napravo skozi odprto okno ali vedno znova izstopiti iz vozila.
Rekreativni lovec in podjetnik Matthias Mähler se je lotil iskanja primerne rešitve za namestitev svojih naprav na zunanji del svojega vozila.
Ko je ugotovil, da na trgu ni primernega nosilca ali stojala, je stvari vzel v svoje roke. Začel je s konstrukcijo prototipa stabilizacijskega in nadzorovanega stojala za nočno opazovanje in termovizijske naprave, ki ga je mogoče namestiti na streho ali okensko steklo avtomobila s pomočjo priseska ali magnetnih nog.
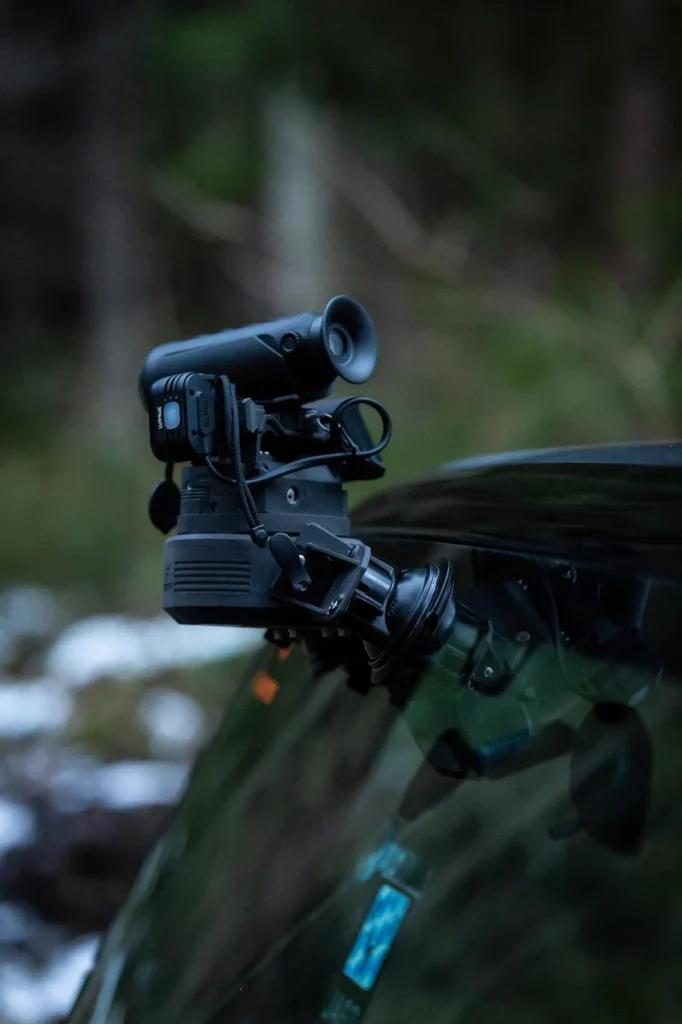
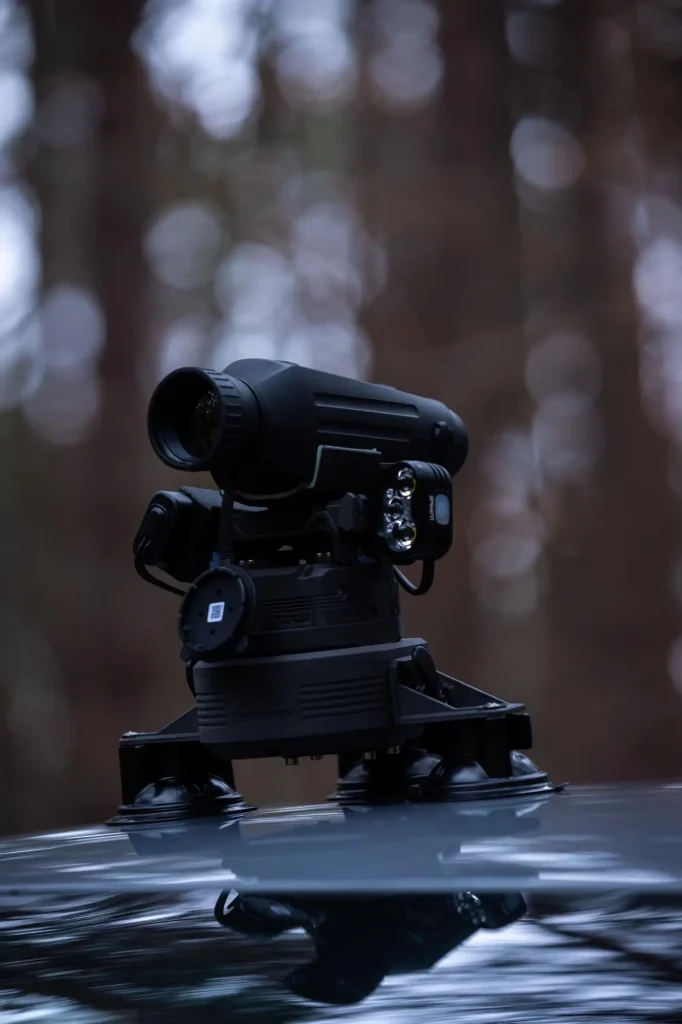
Slika 2: T-Crow XRII z različnimi kamerami na avtomobilskem oknu (levo) in na strehi avtomobila (desno).
Z integriranim vrtenjem za 360° in dodatnim območjem nagiba 55° stojalo T-Crow podjetja XSPECTER omogoča udobno sledenje živalim in oviram iz notranjosti vozila.
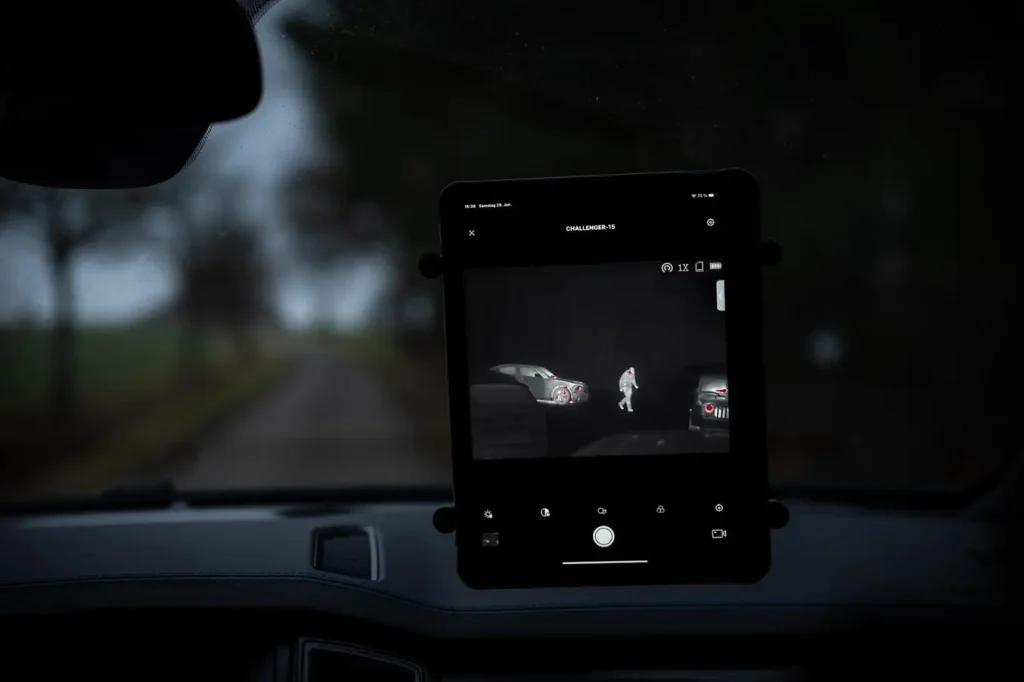
Slika 3: Toplotna slika na zaslonu tablice v avtomobilu.
Od prototipov do serijske proizvodnje
»3D-tiskanje je bilo integrirano v proizvodno linijo, ker sem te tehnologije uporabil za izdelavo prototipov. Delovalo je tako dobro, da smo na koncu oblikovali celoten izdelek z uporabo različnih tehnologij 3D-tiskanja in ga še danes izdelujemo s 3D-tiskanjem,« pravi Mähler.
Najprej je Mähler ponovil več prototipov stojala v sodelovanju s ponudniki storitev 3D-tiskanja na tiskalnikih FDM. Ko je bila izdelana groba zasnova izdelka, je kontaktiral Formlabsovega partnerja za nasvet, katere tehnologije in materiali za 3D-tiskanje bi bili primerni za prvo serijsko proizvodnjo.
Izbral je 3D-tiskalnik Formlabs SLS Fuse 1 in 3D-tiskalnik SLA velikega formata Form 3L za začetek serijske proizvodnje T-Crows s 3D-natisnjenimi deli za končno uporabo.
Serijska proizvodnja s kombinacijo SLA in SLS 3D tiskanja
Pri izdelavi T-Crows se XSPECTER opira na kombinacijo 3D-tiskanja SLA in SLS za izdelavo skoraj vseh komponent za 3D-natisnjeno stojalo za kamero, razen elektronike.
Ohišje je narejeno na Fuse 1. Zahvaljujoč Formlabs materialu Nylon 12 Powder je ohišje lahko in trpežno proti zunanjim dejavnikom. Prav tako je material primeren za naknadno taljenje za vgraditev navojnih puš med montažo.
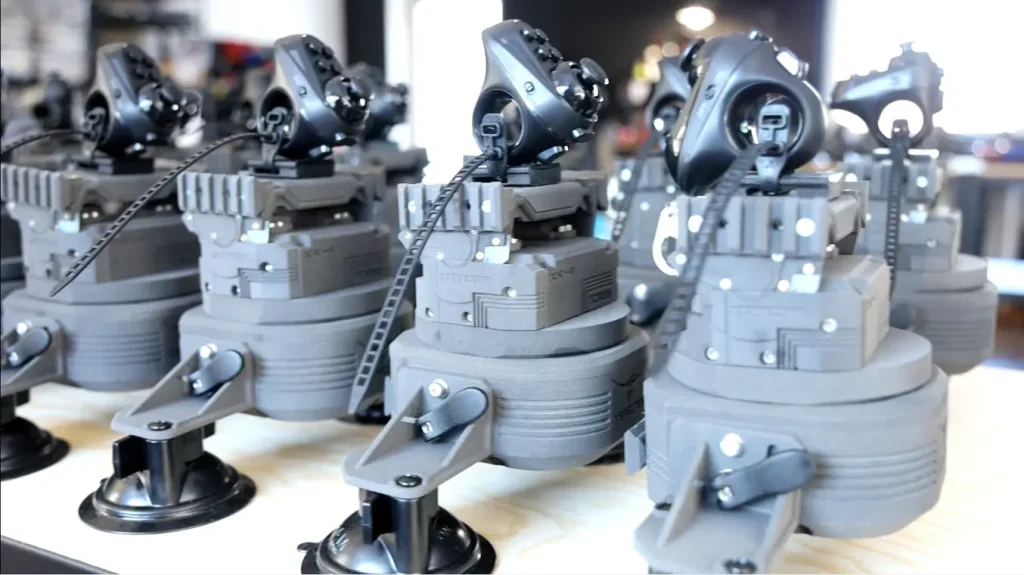
Slika 4: Stativ T-Crow, pripravljen za pošiljanje, z ohišjem, izdelanim iz Nylon 12 Powder
Za osi in zobnike XSPECTER uporabljajo 3D tiskalnik Form 3L in Durable Resin. Fleksibilen, vendar odporen na udarce in z nizkim trenjem; Durable Resin material omogoča namestitev interferenčnih spojin, ki so potrebne za dvoosni krmilni sistem.

Slika 5: Zobniki za T-Crow natisnjeni na Form 3L
Potem ko so vsi posamezni deli natisnjeni in naknadno obdelani v podjetju, se sestavijo z navojnimi vložki in so popolnoma pripravljeni za odpremo v treh dneh.
Prilagodljivost oblikovanja zahvaljujoč 3D tiskanju
Temeljna prednost in ključni dejavnik odločanja za lastno proizvodnjo 3D-tiskanja je ogromna pridobljena prilagodljivost.
Tovrstne konstrukcijske spremembe so narejene na primer pri prilagajanju adapterjev različnih kamer, tako da je stojala mogoče univerzalno uporabljati. Različne oblikovne značilnosti so integrirane neposredno v 3D natisnjeno ohišje. Ko pride na trg nov fotoaparat, lahko podjetje hitro ustrezno spremeni svoj stativ T-Crow in ga proda.
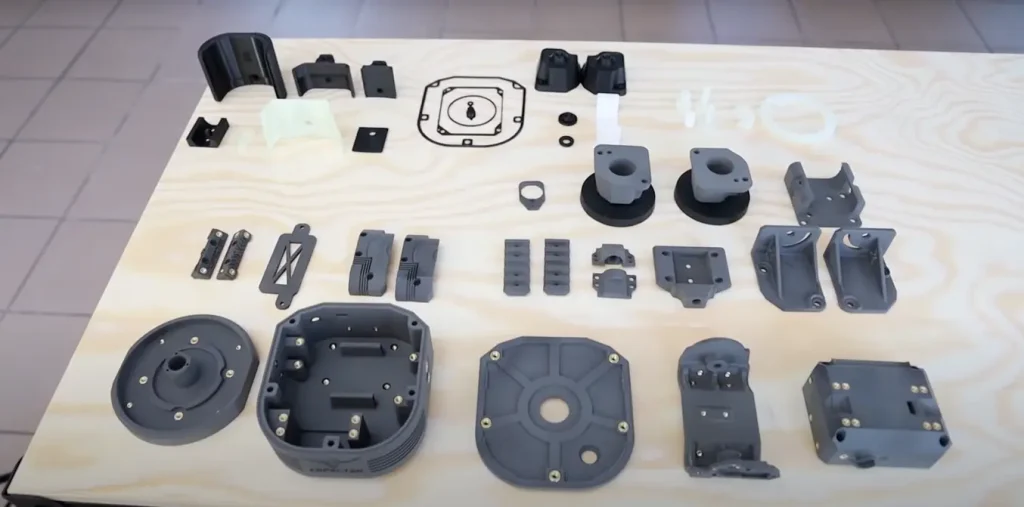
Slika 6: Vse 3D natisnjene komponente T-Crowa pred montažo.
XSPECTER je prav tako prihranil ogromno časa in denarja s hitrejšim odzivom na menjavo dobaviteljev za posamezne dele zahvaljujoč prilagodljivosti 3D tiskanja.
“Nekoč nisem več dobival stikala za vklop/izklop od našega prvotnega dobavitelja in sem ga bil prisiljen zamenjati z drugim. Za nas je to pomenilo, da je bilo treba odprtino za stikalo za vklop/izklop povečati za približno dva milimetra, kar smo spremenil skoraj čez noč,” pojasnjuje Mähler.
Z orodjem za brizganje, ki je bilo na začetku ocenjeno na približno 120.000 €, bi takšna modifikacija prvotnega kalupa zahtevala bistveno več časa in denarja.
Ker XSPECTER s 3D-tiskanjem dosega enako količino ustvarjenih delov, z nižjimi stroški delov kot z brizganjem, hkrati pa se v svoji strategiji močno zanaša na prilagodljivost 3D-tiskanja SLS, si Mähler v bližnji prihodnosti ne more zamisliti nobene druge proizvodne tehnologije za svoj izdelek.
Vir: https://formlabs.com/blog/xspecter-sla-and-sls-end-use-components-production-camera-tripod/